Armature winding is a fundamental aspect of electrical engineering, crucial in the functioning of various electrical machines. This article aims to shed light on two prevalent winding techniques: lap winding and wave winding. In this comprehensive guide, we’ll delve into the difference between lap winding and wave winding, their applications, and their advantages.
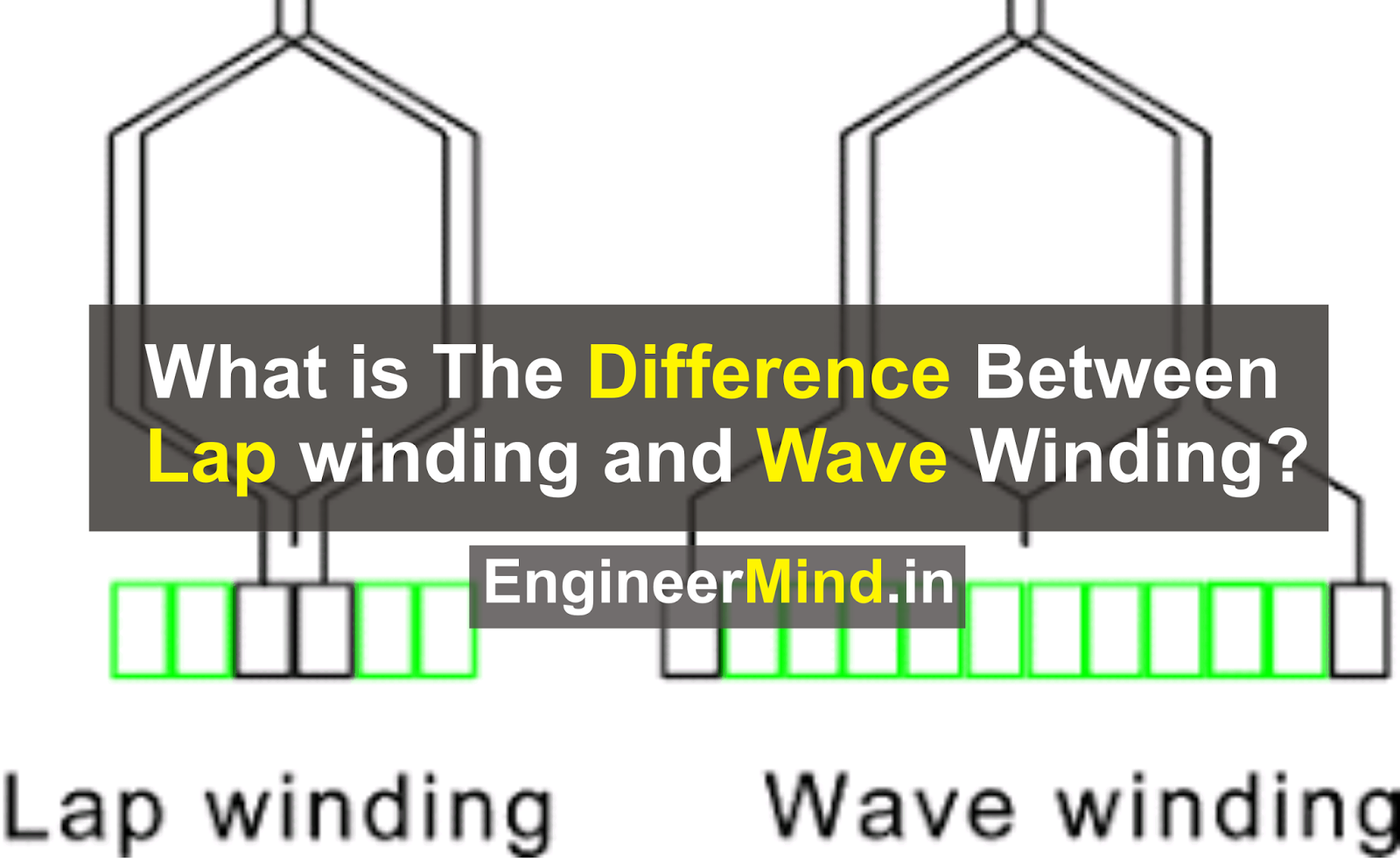
What Is Lap Winding?
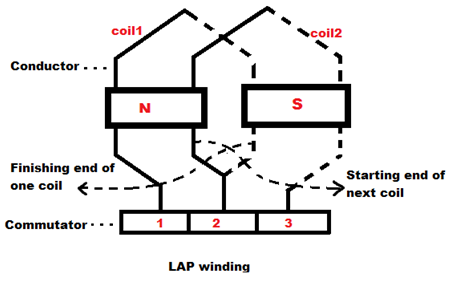
Lap winding, also known as parallel winding, is a method where the end of one coil is connected to the start of the adjacent coil. This creates parallel paths for the current to flow through the armature windings. The key principle behind lap winding is to achieve a high level of redundancy and robustness.
In lap winding, the number of parallel paths (called “parallel paths” or “parallel circuits”) is equal to the number of armature coils. The winding is arranged in such a way that all coils are connected in parallel, forming a closed loop. This design enhances fault tolerance, as a break in one coil does not interrupt the overall circuit.
Advantages Of Lap Winding
Redundancy
Lap winding’s parallel configuration ensures that even if one coil fails or is damaged, the machine can still operate, albeit with reduced efficiency.
High Current Capacity
Lap winding can handle high currents, making it suitable for applications requiring significant power output.
Simplicity
The wiring pattern of lap winding is relatively straightforward, making it easier to manufacture and maintain.
Application Of Lap Winding In Electric Engineer
Lap winding finds applications in a variety of electrical machines, such as:
DC Generators
Lap winding is commonly used in direct current (DC) generators, where its robustness and redundancy are highly advantageous.
Traction Motors
Electric locomotives and other transportation systems often use lap-wound armatures due to their ability to handle high currents and resist damage.
Practical Example of Lap Winding
Let’s consider a practical example to illustrate the concept of lap winding. Imagine a DC generator used in an emergency power supply system for a hospital. In this critical application, lap winding ensures that the generator can continue to function even if one or more coils are damaged during prolonged use.
What Is Wave Winding?
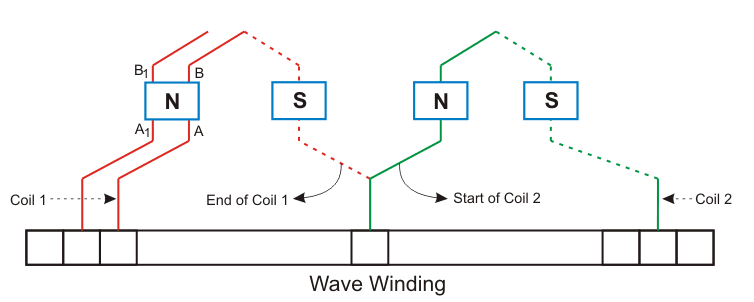
Wave winding, also known as series winding, is a different approach to armature winding. In this method, each coil spans multiple armature slots before continuing to the next coil. Unlike lap winding, where the coils are connected in parallel, wave winding connects them in series, creating a single continuous path for the current.
Wave winding typically involves fewer parallel paths than lap winding. The number of parallel paths is often limited to two, as coils are connected in series to maximize the voltage output.
Advantages Of Wave Winding
High Voltage Output
Wave winding’s series configuration results in a higher voltage output, making it suitable for applications where voltage is a critical factor.
Compact Design
Wave winding allows for a more compact armature design compared to lap winding, which can be advantageous in space-constrained applications.
High Voltage Machines
Wave winding is commonly used in high voltage generators where the goal is to maximize voltage output.
Applications Of Wave Winding In Electric Engineering
Wave winding is employed in various electrical machines, including:
AC Generators
Alternating current (AC) generators often use wave winding to achieve high voltage output.
Small Electric Motors
Wave winding is suitable for small electric motors where compact design and high voltage are desirable.
Practical Example Of Wave Winding
Consider a hydroelectric power station that generates electricity from the flow of water. The generators in such power stations often utilize wave winding to generate high-voltage AC electricity efficiently.
Difference Between Lap Winding And Wave Winding
Overview of Lap vs. Wave Winding
Connection Configuration
Lap winding connects coils in parallel, while wave winding connects them in series.
Redundancy
Lap winding offers redundancy, allowing the machine to continue operating even if a coil fails. Wave winding lacks this redundancy.
Voltage Output
Wave winding results in a higher voltage output compared to lap winding due to its series configuration.
Applications
Lap winding is suitable for high-current applications, whereas wave winding is favored for high-voltage applications.
Comparative Analysis
The choice between lap winding and wave winding depends on the specific requirements of the electrical machine and its intended application. Here’s a comparative analysis to help you make an informed decision:
Lap Winding Pros: Redundancy, high current capacity, simplicity.
Lap Winding Cons: Lower voltage output, larger physical size.
Wave Winding Pros: Higher voltage output, compact design.
Wave Winding Cons: Lack of redundancy, limited suitability for high-current applications.
Factors Influencing Choice
When deciding between lap winding and wave winding, consider the following factors:
Application Requirements: Assess whether your application demands high current or high voltage.
Space Constraints: Evaluate the available space for the electrical machine. Wave winding may be preferred in space-constrained environments.
Redundancy Needs: Determine if the application requires redundancy to ensure continuous operation in case of coil damage.
Conclusion
In the realm of electrical engineering, the choice between lap winding and wave winding is not a one-size-fits-all decision. Each technique offers distinct advantages and is suited to specific applications. Lap winding shines in scenarios demanding redundancy and high current output, while wave winding excels in applications requiring high voltage and a compact design.
Understanding the differences between lap and wave winding empowers engineers and designers to make informed choices, ensuring that electrical machines meet the specific requirements of their intended applications. As technology continues to advance, innovations in armature winding techniques may further refine and expand the possibilities in electrical engineering.
In conclusion, the world of armature winding is as diverse and dynamic as the electrical systems it supports. By comprehending the nuances of lap and wave winding, engineers can drive innovation and efficiency in the ever-evolving field of electrical engineering.